Exploring the Benefits of Injection Molding
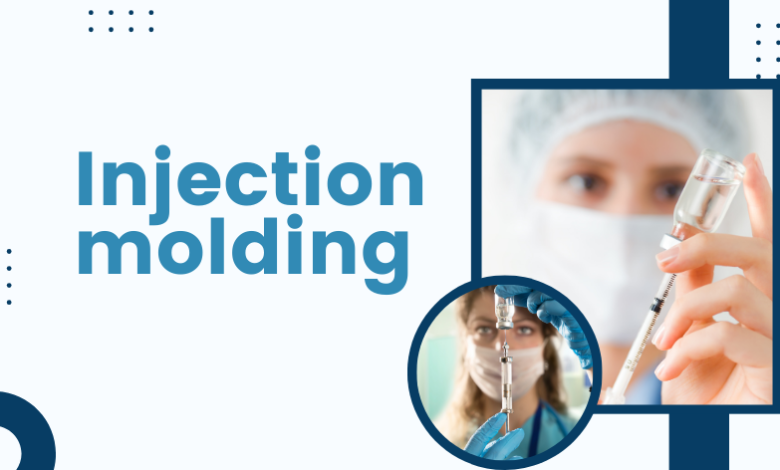
Injection molding is a versatile manufacturing process used to produce plastic parts on a large scale. It involves injecting molten material into a mold cavity, where it solidifies to form the desired shape. This method is widely employed in various industries due to its efficiency, accuracy, and cost-effectiveness.
History and Evolution of Injection Molding
Injection molding traces its roots back to the late 19th century when celluloid, a type of plastic, was first used for injection molding purposes. Over the years, advancements in materials and technology have revolutionized the injection molding process, making it one of the most preferred methods for mass production of plastic components.
Key Components of Injection Molding
Injection Unit
The injection unit is responsible for melting and injecting the material into the mold. It consists of a hopper, barrel, screw, and heater bands.
Mold
The mold, also known as the tool or die, is the cavity into which the molten material is injected. It determines the final shape and characteristics of the product.
Clamping Unit
The clamping unit holds the mold in place during the injection process. It applies the necessary force to keep the mold closed while the material is injected and cooled.
Cooling System
The cooling system helps regulate the temperature of the mold, ensuring proper solidification of the injected material. It plays a crucial role in the overall efficiency of the injection molding process.
Types of Injection Molding
Conventional Injection Molding
Conventional injection molding involves injecting molten material into a mold cavity under high pressure. It is suitable for producing a wide range of complex parts with high precision.
Insert Molding
Insert molding is a variation of injection molding where pre-formed components, such as metal inserts, are placed into the mold before the material is injected. This process is commonly used to encapsulate inserts and create composite parts.
Overmolding
Overmolding involves molding one material over another to create a multi-material component. It is commonly used to enhance product functionality and aesthetics.
Injection Molding Process
The injection molding process consists of several steps, including mold close, injection, cooling, and mold open and ejection. Each step is critical to ensuring the quality and consistency of the final product.
Mold Close
In this step, the mold is closed, and the injection unit moves into position.
Injection
The material is injected into the mold cavity under high pressure and temperature.
Cooling
The injected material is allowed to cool and solidify inside the mold cavity.
Mold Open and Ejection
Once the material has solidified, the mold is opened, and the finished part is ejected from the mold cavity.
Materials Used in Injection Molding
Injection molding supports a wide range of materials, including thermoplastics, thermosets, and elastomers. Commonly used materials include polyethylene, polypropylene, polystyrene, and ABS.
Advantages of Injection Molding
Injection molding offers several advantages over other manufacturing processes, including high efficiency, repeatability, and cost-effectiveness. It allows for the production of complex parts with tight tolerances at a relatively low cost per unit.
Limitations of Injection Molding
Despite its many advantages, injection molding has some limitations, such as high initial tooling costs, long lead times, and limited material selection for certain applications.
Applications of Injection Molding
Injection molding is widely used in various industries, including automotive, consumer goods, electronics, medical devices, and aerospace. It is used to produce a wide range of products, from small components to large, intricate parts.
Recent Technological Advancements
Recent advancements in injection molding technology have focused on improving process efficiency, reducing cycle times, and enhancing part quality. Innovations such as advanced mold designs, predictive maintenance systems, and real-time monitoring solutions have contributed to the continued evolution of the injection molding industry.
Environmental Impact and Sustainability
Injection molding has a significant environmental impact due to the consumption of energy and resources, as well as the generation of waste. However, efforts are being made to improve the sustainability of the process through the use of recycled materials, energy-efficient equipment, and waste reduction strategies.
Future Trends in Injection Molding
The future of injection molding is expected to be shaped by advancements in materials, automation, and digitalization. Trends such as additive manufacturing, smart factories, and sustainable practices are likely to drive innovation and change in the industry.
Challenges and Solutions
Despite its widespread adoption, injection molding faces several challenges, including increasing competition, regulatory requirements, and market volatility. However, manufacturers are addressing these challenges through continuous innovation, collaboration, and adaptation to changing market dynamics.
Conclusion
Injection molding is a highly versatile manufacturing process that offers numerous benefits for producing plastic parts on a large scale. Despite its limitations and environmental concerns, ongoing advancements and innovations are ensuring its relevance and sustainability in the manufacturing industry.
FAQs
- What are the advantages of injection molding over other manufacturing processes?
- Injection molding offers high efficiency, repeatability, and cost-effectiveness compared to other manufacturing processes. It allows for the production of complex parts with tight tolerances at a relatively low cost per unit.
- What materials can be used in injection molding?
- Injection molding supports a wide range of materials, including thermoplastics, thermosets, and elastomers. Commonly used materials include polyethylene, polypropylene, polystyrene, and ABS.
- How does injection molding contribute to environmental impact?
- Injection molding has a significant environmental impact due to the consumption of energy and resources, as well as the generation of waste. However, efforts are being made to improve the sustainability of the process through the use of recycled materials, energy-efficient equipment, and waste reduction strategies.
- What are some recent technological advancements in injection molding?
- Recent advancements in injection molding technology have focused on improving process efficiency, reducing cycle times, and enhancing part quality. Innovations such as advanced mold designs, predictive maintenance systems, and real-time monitoring solutions have contributed to the continued evolution of the injection molding industry.
- What are the future trends in injection molding?
- The future of injection molding is expected to be shaped by advancements in materials, automation, and digitalization. Trends such as additive manufacturing, smart factories, and sustainable practices are likely to drive innovation and change in the industry.